Space frame installation process
1.Lifting process
The project selects mature, safe and reliable hydraulic jacks as the jacking equipment. The jacking bracket draws on the design concept of the bolted ball space frame and tower crane, and takes 1.1m as a standard section. The standard section and the standard section are connected by bolts and disassembled. The installation is convenient; the hydraulic jack is specially made, the lifting capacity is 50t, the height is 2.1m, and the stroke is 1.1m; the hydraulic jack is installed on the bottom base of the jacking bracket, and the upper part is connected with the space frame node and firmly fixed. After checking the safety, start the jacking, and stop the jacking when the space below the bracket is greater than 1.1m, and install the next standard section on the lower part of the bracket (standard section) to the bracket. The support falls on the base below, and the hydraulic jack moves down to lift the support point; continue the next cycle, and repeat the operation, jacking up 1.1m each time, until the space frame is jacked up to the design height.
2.Slit and block ceiling hanging process
The space frame is divided into strip-shaped units with a width of 5 volleyballs. After the ground is lifted and assembled, it is symmetrically suspended to the middle of the sky and closed to form a whole.
- The unit is assembled on the ground from the first row of bolt balls on both longitudinal sides of the space frame, and a temporary support is set up to assemble to the middle of the space frame. Assemble. After assembling each volleyball, add a temporary support under the ball. After checking the temporary support and confirming that it is safe and reliable, disassemble the jacking bracket and move it to the assembled ball. assembled on one side;
- The jacking bracket is raised to a height of 20m, and the lifting part of the space frame is fixed with steel wire ropes to control the arc outstretching of the space frame. One end of the wire rope is equipped with a hand hoist to control the size of the reticulated shell, and a second tension wire rope is added when the space frame is installed to the closing part of the middle plan;
- Then move the jacking device to the starting side, continue to jack up the space frame where the welding ball part is installed, until the jacking device is installed on the bearing ball, use a crane to lift the bearing ball end to the foundation support, After passing the calibration test, the space frame assembled on both sides is hoisted at the same time by a crane in the middle, and the space frame assembled on both sides is closed and connected into a whole in the middle.
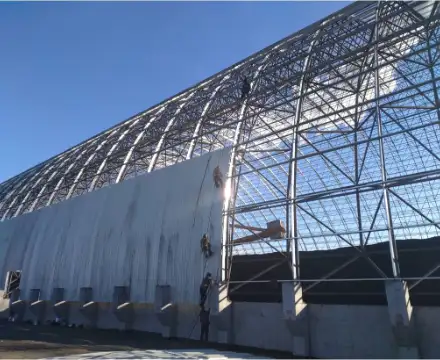
3.Overall jacking process
The unit is assembled on the ground from the first row of bolt balls on the longitudinal side of the space frame, until the assembly and jacking of the space frame to the other side of the foundation support, then move the jacking device to the starting side, and continue to lift and install the welding balls Part of the space frame until it is jacked up to the base support, and after the space frame has passed the calibration and inspection, fix the space frame on the base support.
4.High-altitude bulk method
Use a crane to hoist the small assembly unit to assemble at high altitude, assemble from the installed space frame to the end hemispherical shell from bottom to top, and check the installation accuracy at any time.
5.Key points of space frame installation
- The space frame members and nodes are pre-assembled into units on the ground, which greatly reduces the amount of aerial work;
- Simulate the stress and deformation of the space frame during the construction process through computer technology, accurately arrange the jacking points, determine the jacking sequence, and monitor the jacking process in real time;
- The synchronization of the jacking equipment should be strictly controlled in the jacking process to ensure the stable lifting of the space frame. The space frame of the project is a cylindrical arc reticulated shell structure. With the lifting of the space frame, the jacking device will tilt toward the ground end of the space frame. , The position of the jacking device can be adjusted by adding temporary top support. The jacking equipment is equipped with a large hydraulic cylinder, a temperature control system and an electric synchronous adjustment mechanism. The entire system is controlled by a computer. Servo automatic operation and field bus control and many other technologies, with remote control function, the hydraulic system can be lifted as a whole, or it can be adjusted by separate use to ensure the synchronization of lifting, the error of synchronous lifting, and the distance between each lifting equipment does not exceed 10mm ∕m;
- Before jacking, it is necessary to check whether the force of the rod needs to be strengthened during jacking, so as to ensure the strength and rigidity of the space frame unit. The jacking part of the space frame is fixed with steel wire ropes to control the space frame’s arc-shaped outstretching. The stress condition and setting position of the tight wire rope;
- The size of the space frame strip unit of the ceiling hanging process by strip and block must be checked and reviewed in combination with the strength and stiffness of the grid unit and the capacity of the on-site crane. The projected length of the space frame strip unit with the ball width of every 5 rows of supports is 59m. , 16m in width and about 57t in mass. First lift the ball end of the bearing to the base support with a crane, and then use two cranes to lift the space frame strip units on both sides at the same time in the middle and close them in the middle of the high altitude (about 43m). As a whole, it is required that the crane capacity is ≥200t, the turning radius is 10m, and the lifting capacity is not less than 35t when the arm length is 43.3m, and one 220t and one 260t crane is actually equipped on site.
Measurement and monitoring of reticulated shell construction
The quality of the space frame project mainly controls the deformation of the space frame. The main factors that cause the deformation of the space frame are: installation accuracy and the lifting force of the space frame.
- The size of the space frame unit and the quality of connection (welding) should be strictly controlled in the assembly process, to ensure that the nodes are matched to reduce the cumulative error, and to ensure the assembly accuracy of the reticulated shell. The method of measuring the space coordinates with a diamond-free total station is used to measure the deflection change of the reticulated shell. , Check the vertical and horizontal length of the space frame, grid sag height, measure the center distance of each grid, strictly control the grid center distance, check whether the axis of the reticulated shell is deviated from the axis of the building foundation, ensure that each bolt is tightened in place, weld The ball is in place accurately and adjusted before each fulcrum is removed;
- The space frame structure of the project adopts the multi-point support of the upper chord, and the fulcrum of the jacking is the connection point of the lower chord. The change of the force form can meet the jacking requirements through verification and reinforcement. In order to control the force of the rod during jacking, The force detection of the members of the space frame must be carried out. The project adopts automatic stress monitoring for the force of the space frame. According to the design calculation, an automatic stress system is installed on the members with large force during the jacking process to ensure the lifting of the space frame. During the lifting process, the force of the rod is within a safe range. Through the comprehensive, systematic and whole-process automatic stress monitoring of the upper structure of the reticulated shell, the design input conditions and parameters are monitored, the construction of the reticulated shell structure is guided, the stress changes are grasped in real time, and the net The hidden danger of shell structure, the system has the characteristics of advanced (high precision, automation, all-weather, intelligent operation), stability, compatibility, etc. It can realize remote automatic collection, timing collection, special event collection, etc., wireless transmission, to achieve automation , informatization, real-time and other effects.
Purlin installation process
After the installation of the space frame is completed, the purlins are installed one after another, and the typical sections are installed in bulk and the “ground pre-assembled into tucks and high-altitude tucks” process for installation and comparison. It is recommended to use the process of “pre-assembled on the ground and installed at high altitude” in subsequent installations. The coal bunker of the project has a large span and high height. Considering the crane capacity and labor efficiency, within the scope of the crane operation, the completed purlins are lifted to the For installation at the installation location, outside the working range of the crane, a fixed hoist is used to lift, and a fixed pulley is hung on the upper chord of the reticulated shell, and the hoist is pulled to form a purlin to the installation location for installation.
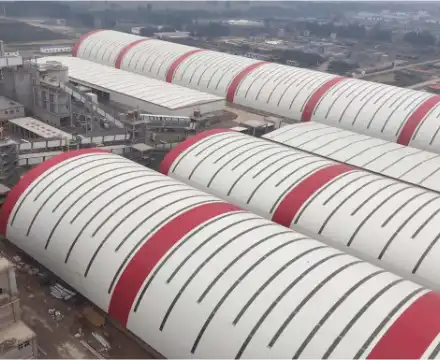
Conclusion
- Combined with the project characteristics and site conditions, in order to speed up the installation efficiency and improve the installation accuracy, the space frame adopts a combination of the overall jacking process, the strip and block top hanging process and the high-altitude bulk process for installation, and the construction is divided according to the expansion joints of the space frame. In the area, the space frame of the straight section is installed by the overall jacking process and the top hanging process by strips and blocks, and the end hemispherical shell and the grid frame of the connecting section are installed by the high-altitude bulk process;
- The purlins are pre-assembled on the ground and installed at high altitudes, which can effectively speed up the installation efficiency;
- During the installation process, the stress and deformation of the space frame during the construction process are simulated by computer technology, and the superstructure of the reticulated shell is fully, systematically and automatically monitored in the whole process. , to ensure installation quality and safety;
- The project overcomes the limitation of space frame installation due to limited construction space, adapts measures to local conditions, and achieves the best energy efficiency of the project. The successful implementation of the project can provide examples and experience for similar projects of water transportation engineering.